In the world of manufacturing, where efficiency and precision are paramount, innovative resource solutions give businesses the competitive edge they need. Manufacturers are constantly seeking ways to streamline operations, increase productivity, and minimize waste, all while maintaining high-quality standards and compliance with evolving regulations. Advanced management systems, real-time data analytics, and the strategic application of automation are key to achieving these goals. Keep reading to explore how modern solutions are transforming the manufacturing landscape.
Streamlining Manufacturing Workflows With Advanced Management Systems
The adoption of advanced management systems is revolutionizing how manufacturing workflows are orchestrated. These sophisticated platforms enable a seamless flow of information across various departments, ensuring that all parts of the production process are interconnected and transparent. This results in reduced errors, lower operational costs, and a solid foundation for making informed business decisions.
At the core of this transformation is the implementation of enterprise resource planning software, which integrates all facets of an operation, from supply chain management to human resources. As these systems become more intuitively designed, they allow managers to adjust production plans on the fly, adapting to new orders or shifts in demand with remarkable agility.
Moreover, these management platforms facilitate better communication and collaboration among team members. With features such as real-time updates and mobile access, employees can stay informed and connected no matter where they are, ensuring that the manufacturing process never skips a beat. This level of integration is creating more resilient manufacturing networks capable of withstanding disruptions and market fluctuations.
Automation and Robotics: Transforming Manufacturing Precision and Speed
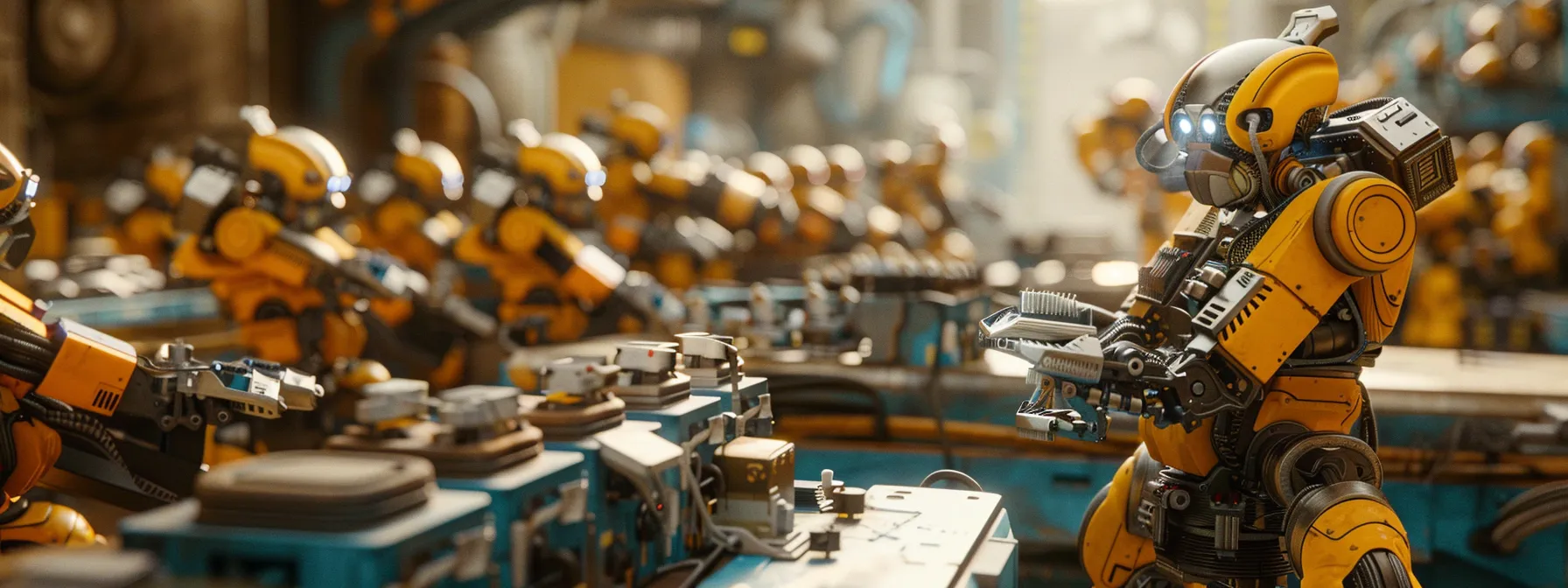
Automation and robotics are terminologies synonymous with modern manufacturing, heralding a new era of efficiency and reliability. Incorporating these technologies into production processes not only accelerates the speed at which products are made but also significantly improves the consistency and precision of output. Robots, for instance, are capable of performing highly repetitive tasks without succumbing to fatigue or the potential for human error.
Another advantage of automation is how it reshapes the workforce. While it does handle tasks formerly performed by humans, it also creates new roles centered around technology management and maintenance. These positions often require a higher skill level, contributing to the development of a more skilled workforce within the manufacturing sector.
Automation also contributes to safer working environments by taking over dangerous tasks. As a result, employees are less exposed to potential accidents, and companies can enjoy a reduction in work-related injuries and associated costs. This emphasis on employee safety is paramount for any responsible business operation.
Sustainable Manufacturing: Leveraging Green Resources for Cost Reduction
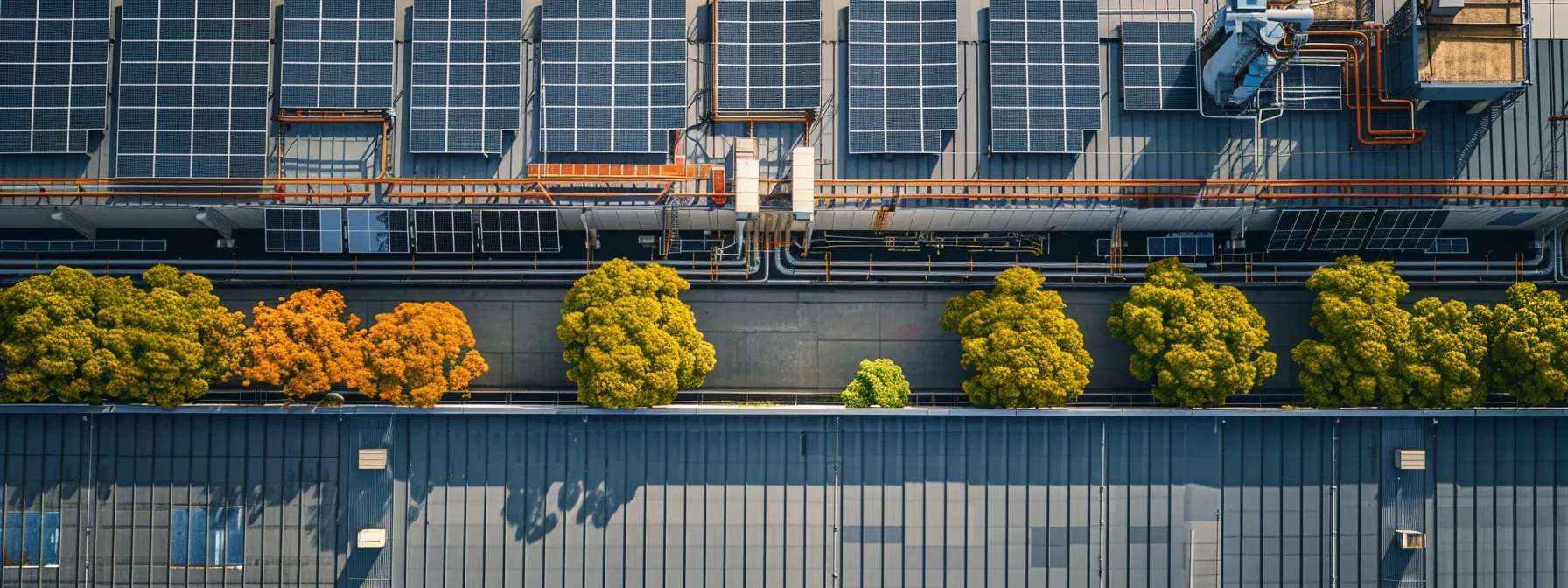
Sustainable manufacturing has emerged as not just an ethical imperative but also a strategic business decision. By leveraging green resources, manufacturers can reduce their environmental footprint while simultaneously cutting costs. Renewable energy sources, such as solar and wind power, are becoming increasingly cost-effective and can offer long-term savings over traditional fossil fuels.
In addition to energy sources, sustainable practices include the adoption of circular economy principles. This approach encourages the reuse and recycling of materials, thereby reducing waste and conserving valuable resources. When manufacturing operations prioritize sustainability, they not only contribute positively to the environment but also improve their public image and appeal to environmentally conscious consumers.
Operational efficiency is often seen hand-in-hand with sustainability. Manufacturers that reduce energy consumption and waste also streamline their processes, making them leaner and more cost-effective. Continuous monitoring and incremental improvements can lead to significant reductions in both carbon footprint and operational expenditure. Well, you can check out the Utility bidder as a solution to energy efficiency and cost saving.
Customized Resource Solutions: Tailoring Operations to Meet Market Demands
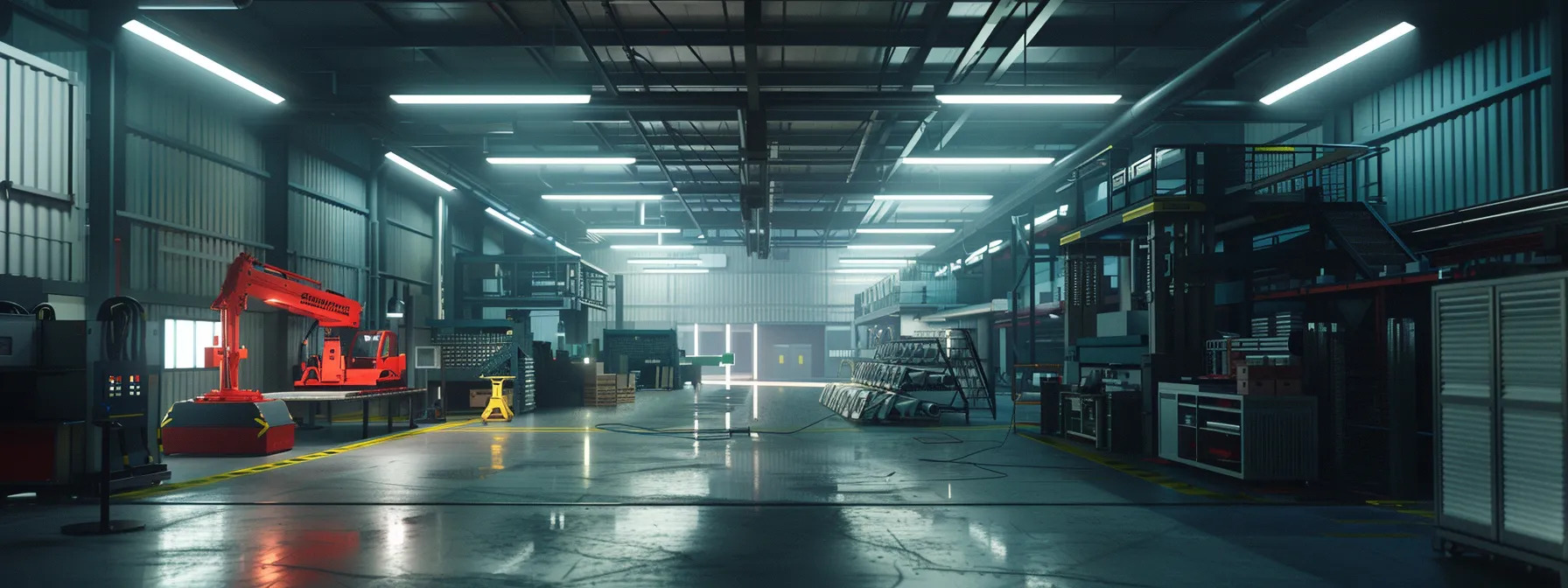
Customization is the final piece of the puzzle in today’s manufacturing strategies. The market demands agility and the ability to tailor operations and products to consumers’ ever-changing needs. By harnessing the power of flexible manufacturing systems, businesses can accommodate personalized product requests and limited-run items without derailing their core production lines.
This bespoke approach, however, requires meticulous planning and dynamic resource allocation. Manufacturers must maintain a delicate balance between custom and standard production to ensure profitability. In this endeavor, real-time tracking and modular approaches to design and build are invaluable, providing the platform necessary for rapid adjustment and innovation.
Overall, modern manufacturers who embrace the merging of advanced management systems, real-time data analytics, automation, sustainability, and customization position themselves for robust growth and success. These resources, when effectively applied, can transform the entire manufacturing process, achieving an unprecedented level of efficiency and customer satisfaction.